
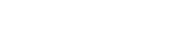



Country Websites
Business Websites
';document.currentScript.insertAdjacentHTML('afterend',preloadTag);
MISTRAS provides an extensive array of non-destructive examination (NDE), maintenance, access, and other integrated asset protection specialties to keep nuclear plants in regulatory compliance and prevent catastrophic failures.
As the energy sectors focus on finding greener energy sources, the nuclear energy industry has become a focal point of development.
Newly-constructed plants must be designed and built in accordance with stringent safety regulations, and existing plants require regular inspection and maintenance of their aging infrastructure to reduce the risk of personnel and environmental damage.
MISTRAS has been providing support for nuclear construction, maintenance, refueling outages, and major component replacement projects for decades. We’ve provided these solutions for various nuclear reactors, including pressured water reactors (PWR), boiling water reactors (BWR), and Canada deuterium uranium (CANDU).
Our inspection, consulting, maintenance, and access solutions enable our nuclear clients to comply with industry regulations, and ensure the safety of plant personnel and the environment.
MISTRAS’ experienced, dedicated nuclear power NDE inspection professionals provide services to this important industry, including inspections for at-height assets with rope access technicians, and certified diving technicians. We specialize in power plant inspections for multiple nuclear components, including:
Our services are supported by our superior quality and safety program, and further enhanced by employing state of the art inspection techniques developed through our RC&A (Research Contracts and Applications) team. Many of these techniques have been sponsored and developed through interaction with the Electric Power Research Institute (EPRI).
MISTRAS NDE services for nuclear plants and assets include:
Multiple industry regulations require that nuclear lift rig heads and internal components undergo regular periodic inspections. NDE is commonly preferred, but the surface inspection technique recognized in ANSI NI 4.6-1978 presents significant problems associated with surface preparation, radiation exposure to inspection personnel and disassembly/reassembly of the lifting rigs.
MISTRAS lift rig inspection solutions require no overload or rig disassembly, while inspecting 100% of rig components, helping our clients achieve regulatory compliance and enhance safety while keeping downtime to a minimum.
During normal operations, once-through steam generators (OTSG) and recirculating steam generators (RSG) are subjected to a variety of stresses that can cause asset degradation that can lead to serious safety and productivity consequences. Some of the more common steam generator defects include:
MISTRAS NDE capabilities allow nuclear steam generators to be inspected while assets remain in-service, which limits costly facility downtime, reduces the safety hazards, and protects asset integrity.
MISTRAS utilizes multiple steam generator inspection services to provide asset owners with a comprehensive understanding of their steam generator’s condition, including:
Heat exchanger tubing is specifically subject to wall loss, cracking, erosion, pitting, and leaking, often due to the difficulties in detecting damages hidden deep inside hard-to-see tubes. MISTRAS is equipped with multiple inspection solutions to detect and repair these damages.
Utilizing eddy current (EC) inspection technology, MISTRAS inspects in-service and newly-manufactured heat exchangers. EC can help nuclear clients identify damaged tubes before they fail, and can inspect well over 1,000 tubes a day with minimal equipment downtime.
Our Twisted Tube heat exchanger inspections enable technicians to accurately and confidently inspection twisted tubing in real-time, with the ability to detect small defects, such as stress corrosion cracking. These inspections utilize full-length recording capabilities and offline data analysis to assess damages with the customer.
MISTRAS other heat exchanger condition assessment and repair services include:
Flow-Accelerated Corrosion (FAC) is a serious defect in nuclear facilities that can lead to decreased production and even complete asset failure.
The protective oxide layer dissolves in the flow of materials, which increases the rate of metal loss and degradation. Given that flow accelerated corrosion occurs on the inside of piping, it can be extremely hard to detect.
MISTRAS has developed an NDE inspection program that utilizes our wide range of available NDE technologies. We help our clients detect and locate flow-accelerated corrosion within the piping of nuclear facilities quickly, accurately, and non-intrusively, which decreases the costs and risks associated with traditional inspection methods.
MISTRAS Cavity Leak Detection services detect and isolate leaks in the reactor cavities, transfer canals, and spent fuel rod storage pools of nuclear power plants.
Leaking materials in nuclear facilities create a huge safety risk for plant personnel, along with slowing facility production and increasing the risk of a costly shutdown. MISTRAS NDE technology is extremely sensitive, with the ability to identify even the smallest leaks as soon as they occur, allowing operators to prevent more serious damage from leaks left undetected.
MISTRAS has also successfully completed diving projects to install waterproof lining on the walls of the spent fuel pool of a nuclear power plant. MISTRAS’ certified diving technicians designed, manufactured, and installed a flexible, underwater sealing membrane system to compensate for the expansion of concrete due to alkali-aggregate reaction.
MISTRAS Balance of Plant (BOP) Services ensure that the auxiliary systems in nuclear power plants are operating efficiently and remain free of damage. BOP systems outside of the core nuclear steam supply system are still essential to plant operations, so it is essential that these systems are regularly inspected and maintained to promote optimal production capacity.
Some of MISTRAS’ BOP Services include:
MISTRAS' teams also perform a wide variety of maintenance and mechanical services for nuclear power plants, including using trained rope access technicians and V-Deck suspended work platforms for at-height assets. Our services include:
Many assets in nuclear plants are not able to be easily accessed for regular inspection and maintenance due to high temperatures and radiation concerns. For these assets, MISTRAS recommends permanently-installed monitoring systems that track asset conditions, to ensure damages do not appear and worsen in between scheduled inspections.
MISTRAS offers monitoring solutions to track:
Loose Parts: MISTRAS helps to detect metal-to-metal impacts in reactor cooling systems, using advanced, real-time alarm discrimination to avoid false alarms. If undetected, loose parts can cause flow blockages, RCS boundary integrity issues, and weakening of safety-related components.
Valve Flows: Our valve monitoring solutions keep tabs on flow conditions on critical valves in nuclear plants, including main steam isolation valves and power-operator relief valves.
High Energy Piping (HEP): enables plant operators and maintenance personnel to remotely detect micro- and macro-cracking, flow noise variations, and thermal fatigue and thermal expansion in high energy piping.
With extensive nuclear industry engineering expertise, MISTRAS technicians can provide consulting services to support all aspects of your nuclear facility, including:
Our experts provide quality assurance and promote efficient plant operation while ensuring personnel and facility safety. MISTRAS consultants are cognizant of relief requests that can reduce the scope of internal stress testing in areas such as containment spray pump testing, safety injection check valve testing, and skid mounted positions, among others.
Some of our many consulting services include: