
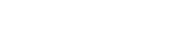



Country Websites
Business Websites
';document.currentScript.insertAdjacentHTML('afterend',preloadTag);
MISTRAS’ integrated data management approach for pipeline integrity proactively uses acquired data and expertly-developed software to assess pipelines and predict future risk based on historical data to help ensure the future of asset integrity.
It can be difficult or even impossible to know what issues a pipeline will encounter while in service, particularly when operators do not have access to all relevant historical integrity data. Most pipeline operators do not have access to advanced software that can examine pipeline data to accurately gauge the amount of risk that an asset may experience.
Being unaware of risk and spill possibilities has led to pipelines being installed in high-risk areas that are highly-sensitive or overwhelmingly residential. MISTRAS Group, New Century Software™ by MISTRAS, Integrity Plus™ by MISTRAS, and Onstream offer extremely-valuable and accurate solutions for avoiding pipeline damage and potential harm. Our integrated application capabilities and analysis software enable predictive analytics to keep operators steps ahead of damage. Once data is collected and stored, maintenance and mechanical efforts are decided through what is analyzed from that information.
Having access to a full set of historical non-destructive testing (NDT) and inline inspection (ILI) directly influences predictive data analysis within the data management journey. Being able to effectively access stored data in an asset performance management (APM) application makes analyzing data more effortless as all information is one place.
Digital reporting solutions can feed newly-acquired data directly into an APM and GIS applications and combine it with pre-existing inspection data, helping to ensure operators have access to their asset’s complete set of integrity data can be used as actionable information to maximize safety, enhance productivity, and optimize budgets.
As the industry moves towards data-driven, risk-based IM programs, data can be used to perform criticality assessments to determine an identified defect’s probability and consequence of failure. Integrated APM and GIS solutions for risk assessment from New Century Software and Integrity Plus eliminate the need to ship data offsite and data more accessible.
MISTRAS' PCMS™ offers a risk-based inspection (RBI) module, using inspection data to feed an RBI calculator to help operators make informed decisions on potential risks. The digital data that has been acquired through mobile reporting is used to inform these applications and makes predicting any kind of pipeline integrity possible.
Value-Added Solutions: Integrated ILI & GIS Data
Onstream and New Century Software work together to bring integrated, value-added solutions to your pipeline operations. ILI data can be used to construct features in a GIS. This is beneficial when GIS data is poor quality, or a pipeline does not exist in a customer GIS. The ILI is used for the derivation of centerline data. As-built data can also be used to construct these features.
For centerline data in a GIS that is poor quality when other customer data is reliable, the GIS centerline, including spatial geographic and linear recurring sequence (LRS) corrections, can be corrected. ILI data is loaded into a preferred GIS table structure to correct this data.
ILI alignment sheets can be generated with pipe tally reports and GIS data. Sheets are beneficial when Operators need to review aligned ILI data with pipe material, map band, elevation profile, class locations/high consequence areas (HCAs), close interval survey, ECDA, crossings, and other data.
GIS data like HCA, class location, coating, test pressure, and more can also be added to a pipe tally to add additional attributes dynamically segmented for each record. The GIS can also be updated with missing pipe features when the data in the system does not match ILI data. Missing casings, bends, wall thickness changes, taps, and more that don’t appear in a GIS can be updated for consistency with ILI data.
ILI runs of the same of different vendors can be compared and displayed on an ILI alignment sheet. This process assumes that pipe tallies have already been aligned. Girth weld comparison reports are possible from ILI inspections to see joint-by-joint comparison of two or more runs. The report will show sequential joints that are matched or mismatched.
HCA analysis for liquid or gas pipelines can help determine class location and HCA using the potential impact radius (PIR) method along the pipe centerline. Liquid operators need to determine spill impact analysis for segments that are within an HCA. All the ways ILI data is being used to add value to pipeline operations is the true potential of integrated data acquisition.
Predicting what risks a pipeline can encounter is often difficult or even impossible to determine. Spatial Risk Analyst from New Century Software helps measure risk along a pipeline with customized algorithms, lending insight into the vulnerabilities of pipeline segments.
Spatial and tabular data can be used in the program as it runs a wide variety of risk models. Our Gas HCA Analyst software can work jointly with Spatial Risk Analyst for automation and error reduction.
Knowing the risk along a pipeline is essential in meeting regulatory compliance standards and helps to inform decisions.
Learn more about Spatial Risk Analyst.
Spill Impact Analyst is a game-changer for developing response plans for mitigation. Modeling allows operators to view pipelines with defect information. The program features evaluation for leak potential, predicts volumes, and assists in plan creation in the case that a leak does occur.
This GIS extension uses a flow analysis engine to predict spill spread and speed, as well as high consequence areas (HCAs) in the proximity. The Spill Impact Analysis benefits greatly reduce cost for operators, as spills are conquered before they have the chance to happen.
Learn more about Spill Impact Analyst here.
Data from inspection is integrated with pipeline GIS and asset information with InTrack. This solution allows anomalies to be viewed in a GIS which leads to assessment plans being formed. Developed to handle of large data sets, this program is a useful tool in planning future work that can prevent pipeline failure.
Post-inspection enhanced analysis services can provide pipeline operators with additional information to support critical integrity decisions. These services reveal information such as dent strain and restraint, bend strain, and pipeline movement. Corrosion growth is also a huge factor that is determined through matching assessments.
In addition to offering traditional box-to-box and signal-to-box corrosion growth matching, we also offer signal-to-signal corrosion growth services that take successive data sets and align the two inspections in terms of welds and anomaly signatures. Signal-to-signal matching also normalizes the signatures at each joint to compensate for changing run conditions or tool variations. The method resizes the matched, normalized anomalies with the same algorithms and methodology to remove analysis bias.
This process results in a more accurate corrosion growth assessment that eliminates uncertainty out of corrosion growth rates and identification of active corrosion.