
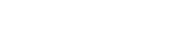



Country Websites
Business Websites
';document.currentScript.insertAdjacentHTML('afterend',preloadTag);
Leaks can happen in any of your assets that carry or transport liquids or gases, which both wastes costly resources and presents a safety risk for facility personnel and the surrounding environment.
Corrosion, erosion, vibration, thermal changes, and any other causes of stress can lead to the creation of leaks in refinery, power, and process plant assets.
Especially when dealing with potentially hazardous materials, ensuring that assets remain leak-free is essential in maintaining adequate plant safety and avoiding injury. Gone undetected, leaking assets waste valuable resources, which can add up to huge losses for your facility over time.
Leaks frequently occur in a variety of assets and equipment, including:
Gas leaks are an especially dangerous defect in your facility because of how difficult they can be to detect.
Crude oil contains hydrocarbons that can be highly-flammable even in low concentrations. In oil & gas refineries and petrochemical facilities, escaped hydrocarbons (including methane, hydrogen sulfide, ethane, butane, and many others), can be toxic, flammable, or otherwise hazardous, but are often invisible to the human eye.
Many of these gases are lighter than air, so when allowed to leak from their designated containers, they will rise and potentially come into close contact with flare stacks.
Steam leaks are detrimental to any facility that uses steam as an element of power generation processes.
Leaking steam results in energy losses, which decreases the production of the entire facility. Pressure losses from leaking steam decrease production capacity and can cause additional problems within associated componentry of steam systems.
Steam leaks are difficult to detect, and even minuscule steam leaks that are impossible to see can cause extreme burns upon contact, creating a risks for facility personnel.
A wide variety of defects can degrade a material enough to cause a liquid leak in an asset. Corrosion, cracking, metal embrittlement, and other damage that decreases material thickness and strength can cause a leak to occur. Assets that are particularly at risk for liquid leaks include:
In addition, faulty equipment or incorrect design and installation can create potential leaking, especially in joints, flanges, valves, and welds.
MISTRAS maintains a wide variety of non-destructive testing (NDT) solutions to detect, source, repair, and prevent leaks in your facility.
As world leaders in Acoustic Emission (AE) technology, MISTRAS’ inspection and monitoring systems and services help our clients not only detect leaks, but also pinpoint their location and quantify leakage, providing facilities with the information needed to make more informed maintenance decisions.