
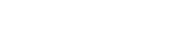



Country Websites
Business Websites
';document.currentScript.insertAdjacentHTML('afterend',preloadTag);
Fatigue is the result of residual stress affecting an asset’s composition, including stresses from temperature, corrosion, load, and a variety of other factors.
Over time, assets of every material experience fatigue-related wear from operational use and the conditions of their surrounding environment. As assets age, fatigue increases, risking the onset of fatigue-related defects and flaws, the most common of which are cracking, thinning, and reduced strength.
In general use, assets should be regularly inspected for the symptoms of fatigue in order to ensure that equipment and componentry remain safe, efficient, and fit for use.
Thermal fatigue is caused by cyclical stresses resulting from fluctuations in temperature, spatial temperature gradients, and constrained high-temperature areas. Thermal expansion results in surface cracking within componentry, which, if left untreated, can quickly spread and result in catastrophic damage to an asset.
Thermal fatigue can occur without the stress of a mechanical load on an asset, affecting especially those places that are subject to a variety of conditions, environments, and temperature changes, found frequently in:
Corrosion fatigue is a common defect caused by the combination of cyclic stress and a corrosive environment. Fatigue in a material causes cracking, which is then accelerated by surrounding corrosion, meaning that defects can occur quickly and at lower loads.
Corrosion fatigue is common in a variety of assets, including:
Wherever there are defects or irregularities in a material surface, such as pits, notches, joints, and changes in metallurgy, corrosion can collect and increase the likelihood of fatigue-related cracking.
Vibration fatigue is a type of mechanical fatigue that affects any asset that experiences vibration during operation, so it is most commonly affects rotating equipment.
Vibration causes a material to undergo dynamic stress, which can weaken components over time and lead to load-related flaws. When an initial crack is created, further vibration can quickly propagate cracking into a larger issue. Materials maintain an endurance limit for the amount of load they can safely withstand, and vibration fatigue occurs when that endurance limit is surpassed.
Vibration fatigue is common in any assets that regularly withstand high levels of movement, such as:
Aircrafts undergo intense stress during operation. Both engines and aircraft shells are subject to componentry fatigue that hinders operation and can lead to total failure.
The rapid temperature and pressure changes that aircraft componentry undergoes makes it subject to fatigue and cracking which can damage planes to the point of being unsafe for use. Microscopic cracking can be difficult to detect with visual inspection yet still damaging to an aircraft. Types of fatigue that engines and shells can experience include:
Structural fatigue plagues bridges, buildings, and other large infrastructure. Traffic, use, weather, temperature, and other factors create dynamic loads that put a strain on materials and structures. Metal structures are especially vulnerable to structural fatigue given that welds can weaken and degrade over time.
Structural fatigue can cause cracking and other defects that reduce asset strength, which is particularly dangerous for load-bearing infrastructure assets that are crucial for our transportation systems. Over time, structural fatigue can be initiated and accelerated by a variety of influences that occur in daily use, risking structural insecurity or even complete asset failure if left untreated.
MISTRAS offers solutions to quickly and accurately identify fatigue in your assets before it manifests itself in more serious damage. Our non-destructive testing (NDT) inspection technology can inspect your assets non-intrusively while they remain in service, reducing inspection time and costs.
With a wide base of available inspection solutions, engineering expertise, and access capabilities, we can identify asset fatigue in any environment. Some of our fatigue solutions include: