
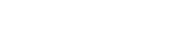



Country Websites
Business Websites
MISTRAS Non-Intrusive Inspection (NII) special emphasis programs integrate our inspection & engineering services capabilities to provide a safe and cost-efficient alternative for pressure equipment inspections.
Non-Intrusive Inspection is a thorough and comprehensive inspection strategy, through which MISTRAS performs non-destructive testing (NDT) inspection on pressure equipment completely externally, eliminating the need for vessel entry during any phase of the inspection process.
NII programs are a safer, more cost-efficient alternative to time-intensive inspection programs that require asset entry to inspect areas of potential concern.
NII programs are proven to be effective in detecting asset integrity concerns including corrosion, cracking, hydrogen damage, and welding flaws in a variety of equipment, including:
As a OneSource provider of asset protection solutions, MISTRAS Group supplies expert engineers and certified technicians to design, implement, and custom-tailor NII program customized to your facility’s needs.
MISTRAS NII special emphasis programs are broken down into a series of clearly defined steps:
At the start of a non-intrusive inspection program, MISTRAS engineers will complete an extensive integrity review of the asset. During this review process, we compile background information about the asset to determine whether NII is feasible, dividing equipment into zones rather than observing it as a whole for a more in-depth componentry analysis.
During NII integrity reviews, MISTRAS engineers analyze:
Based on the conditions and requirements of the asset, MISTRAS engineers will select the most appropriate inspection methodologies for your facility.
Using the information gathered in the integrity assessment, damage analysis, and risk based inspection (RBI) data, the team develops an inspection plan tailored to your equipment.
As a true OneSource provider, MISTRAS will service your asset from start to finish, offering rope access crews, mechanical services, insulation removal, surface preparation, and any other services that accompany the inspection of your assets.
The inspection process is divided into three categories—A, B, and C—based on the severity level of expected degradation within the asset. Once the inspection plan has been set in place, MISTRAS techs complete the NII process on your equipment with an emphasis on safety, efficiency, and cost reduction.
Our technicians will select the correct inspection technique for your asset from our long list of NDT capabilities, including:
All integrity and inspection data is compiled into a final inspection report summarizing the process and findings of the procedure, which can be used for further analysis and evaluation.
The engineering team will also create a plan for future inspection based on the findings and the predicted degradation rate of the asset, and may recommend additional condition-monitoring as a good practice for reducing risk of operation.
What's Next?
Questions? Speak to our Non-Intrusive Inspection (NII) experts today.
Contact a MISTRAS expert