
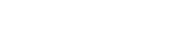



Country Websites
Business Websites
Popular Searches
Branch Locator
Oil & Gas
Field Inspections
Sensoria™ Wind Blade Monitoring
Pipelines
MISTRAS Digital®
Traditional Non-Destructive Testing (NDT)
Careers
Events Center
ART Crawler
Aerospace & Defense
Investors
Environmental, Social & Governance (ESG) Initiatives
Equipment
Consulting
Training