
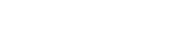



Country Websites
Business Websites
';document.currentScript.insertAdjacentHTML('afterend',preloadTag);
MISTRAS Group is a leading designer and manufacturer of non-destructive testing (NDT) equipment for industrial asset protection, including solutions for spot inspections and long-term, unattended monitoring applications.
MISTRAS develops and manufactures leading-edge NDT technologies, specializing in advanced acoustic emission (AE) equipment, that enables our clients to stay informed of their assets' conditions.
MISTRAS has been designing and manufacturing innovative AE inspection equipment since 1978. It’s how the company got its start, and MISTRAS has burgeoned an industry world leader on the backbone of our AE equipment portfolio’s success.
Today, MISTRAS' legacy of AE equipment innovation remains. MISTRAS offers a full range of AE inspection equipment, including:
Learn more about our AE equipment here.
We manufacture our equipment in our world headquarters in Princeton Junction, NJ – USA, operating to a strict ISO 9001: 2015 National Quality Assurance (NQA)-approved quality management system (QMS).
MISTRAS employs some of our industry’s leading scientists, who build on MISTRAS’ culture of intensive scientific research & development.
Much of our equipment has been developed in tandem with our customers and leading industry organizations, who recognize MISTRAS’ history of technological innovation and commission our help to solve their most difficult asset protection problems. By working hand-in-hand with our clients, our technology is designed to detect the defects and discontinuities that our customers deal with most.
Offering both handheld and permanently-installed monitoring equipment, we provide the tools and the training that our clients need to stay informed of their assets' conditions at all times. If our clients suspect their piping is corroding, their bridge cables are fretting, or their valves are leaking, our equipment enables them to get the answer immediately, rather than waiting for their service provider to arrive onsite and potentially allowing a bad situation to get worse.
We provide inspection and monitoring equipment to clients in many industries, including: