
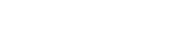



Country Websites
Business Websites
';document.currentScript.insertAdjacentHTML('afterend',preloadTag);
MISTRAS’ mechanical wear, fatigue, and crack detection online monitoring solutions help you maintain equipment health, extend asset life, and minimize unexpected failures.
Proactive monitoring of mechanical wear, fatigue, and cracking is vital in preserving asset integrity and minimizing operational risks. Across industries, rotating machinery, structural supports, and load-bearing components are subject to cyclical stress and harsh operating conditions. Over time, these forces contribute to the formation of cracks, material fatigue, and worn components, which can escalate into significant hazards if undetected. By implementing advanced mechanical wear, fatigue, and crack detection strategies, organizations strengthen their predictive maintenance programs, reduce the risk of unplanned outages, and improve overall operational safety.
MISTRAS’ mechanical wear, fatigue, and crack detection services incorporate a variety of diagnostic techniques designed to identify potential vulnerabilities before they lead to failure. Cutting-edge acoustic emission (AE) monitoring tracks the sound waves generated by material defects, while vibration analysis measures subtle changes in equipment movement that can signal bearing wear or shaft misalignment. In tandem with MISTRAS’ expansive non-destructive testing (NDT) portfolio, these technologies provide a clear picture of asset health at every phase of operation.
Fatigue manifests through cumulative stress cycles, causing microcracks that expand over time. Frequent load changes in rotating equipment—such as turbines, gearboxes, and pumps—can gradually weaken metal structures. Meanwhile, stationary assets like bridges or structural frameworks experience repeated stress from environmental factors and dynamic loads. By continuously monitoring stress anomalies and detecting the earliest signs of crack propagation, MISTRAS helps clients pinpoint emerging flaws and make data-driven decisions about asset maintenance or replacement.
Common Applications of Mechanical Wear, Fatigue & Crack Detection
Through proactive strategies and ongoing diagnostic evaluations, operators can maintain high-performing mechanical systems that offer safer, more reliable operations. Furthermore, data gathered from monitoring technologies supports both short- and long-term planning, driving continuous improvement in maintenance regimes and lifecycle management.
MISTRAS emphasizes comprehensive asset management, integrating mechanical wear detection, fatigue analysis, and crack monitoring into a broader condition monitoring framework. This holistic approach ensures that interconnected issues, such as temperature fluctuations and electrical anomalies, do not go overlooked. By examining all aspects of an asset’s performance, maintenance decisions become more targeted, efficient, and cost-effective.
Ultimately, prioritizing mechanical wear, fatigue, and crack detection safeguards critical systems and infrastructure. With regular condition assessments, real-time data collection, and expert interpretation of inspection results, MISTRAS empowers organizations to proactively address defects and sustain safe, uninterrupted operations.