Risk-Based Inspection (RBI) prioritizes inspections and maintenance based on the likelihood and consequences of equipment failure. It helps optimize resource allocation, enhance safety, reduce costs, and extend asset life through data-driven decision-making.
Risk-Based Inspection (RBI) is a strategic approach to managing the maintenance and inspection of assets, designed to prioritize resources based on the likelihood and consequence of failure. This methodology focuses on identifying assets with the highest criticality and determining the most effective inspection schedules to mitigate risks. RBI is built around evaluating both the probability of failure and the potential impact on safety, the environment, production, and costs.
MISTRAS’ expertise in asset integrity management helps ensure that companies can accurately assess risk levels and schedule inspections in a way that reduces unnecessary costs while maintaining safety and operational reliability.
The primary goal of RBI is to optimize the inspection process by aligning resources with the areas of greatest risk, ensuring that high-priority assets receive the attention they need while reducing unnecessary inspections of lower-risk components. It incorporates various factors such as historical data, equipment type, operational conditions, and environmental influences. By combining engineering judgment with data-driven insights, MISTRAS' RBI solutions help to ensure that assets are maintained safely and efficiently while minimizing downtime.
Key Benefits of (RBI) Include:
- Achieving better mechanical integrity Mechanical Integrity (MI) and equipment reliability
- Minimizing downtime by preventing unplanned outages
- Reducing safety risks
- Optimizing inspection and maintenance costs
- Focusing resources where they’re most needed
- Improving budgeting and planning for future inspections and maintenance
- Streamlining turnaround planning
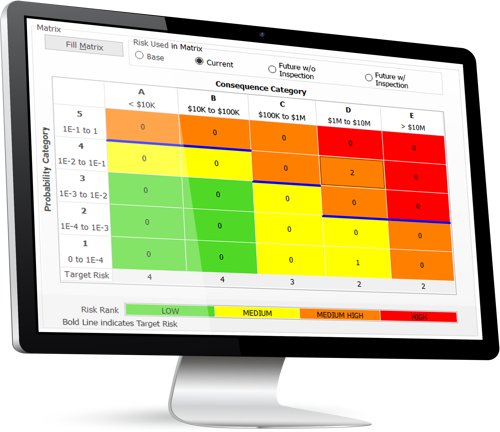
Risk-Based Inspection (RBI) Assessments
MISTRAS’ (RBI) approach incorporates both semi-quantitative and qualitative methods to assess risks, offering a balanced and precise evaluation of your assets. This methodology allows you to identify the most critical areas and prioritize inspections based on the risk they pose.
Key RBI Services Include:
- Semi-quantitative and qualitative approach: A blend of expert judgment and calculated risk assessment to tailor strategies to your operations.
- Implementation, Revalidation, and Updates: We support the entire RBI lifecycle, from initial implementation to ongoing updates and revalidation to keep your maintenance program aligned with evolving operational conditions.
- PCMS RBI/IOW Modules: Our proprietary modules help centralize your risk data, streamline inspection schedules, and ensure your maintenance program is always up to date.
Damage Mechanism Review (DMR)
MISTRAS leverages its extensive experience in conducting API 970 Damage Mechanism Review (DMR) to identify potential corrosion threats. MISTRAS engineers use proven methodologies to assess how various environmental and operational conditions (such as temperature, pressure, and chemicals) contribute to corrosion risks. These reviews form the foundation for the development of targeted corrosion mitigation strategies.
Systematic review of corrosion susceptibility: A structured approach to identify and assess the corrosion risks your equipment faces based on operational and environmental conditions.
- Identification of corrosion rates and damage mechanisms (DM): Detailed analysis of the expected corrosion rates and the damage mechanisms that may affect your assets, ensuring you’re prepared for potential threats.
- Consideration of Integrity Operating Windows (IOWs) for monitoring: We incorporate IOWs into the (DMR) process to ensure continuous monitoring of equipment within safe operational limits.
Corrosion Control Document (CCD)
To further mitigate corrosion risks, MISTRAS offers expert assistance in creating and updating Corrosion Control Document (CCD) tailored specifically to your assets. These documents ensure that your equipment is protected in accordance with industry standards and best practices.
- CCD development and update: We develop and update CCD to reflect the latest industry standards and your plant’s operating equipment and environments.
- Customized to client requirements: Each CCD is fully customized to meet the unique needs of your operation, helping you safeguard your assets in a cost-effective and compliant manner.
Integrity Operating Window (IOW)
Integrity Operating Window (IOW) are vital for maintaining safe and efficient operations in complex systems like refineries and other process plants. MISTRAS delivers expert consulting on defining IOW, helping companies define and manage operational limits and process parameters, and proactively respond to deviations to help prevent equipment failure.
- Identify process parameters, limits, and actions: Defining the key process parameters for your equipment and set clear operational limits and response actions.
- IOW excursion and response procedure: Development of clear response procedures for (IOW) excursions, enabling swift and effective action to prevent failure.
- Operational data analysis and trending: Analysis of operational data to detect trends and deviations, providing early warnings and helping mitigate risks before they become critical issues.
By leveraging MISTRAS Group’s tailored RBI services, DMR checks, CCD development, and IOW management, plant operators can improve asset reliability, reduce downtime, better management inspection and maintenance resources, and maximize the safety of your operations.